As good as new: Retrofitting Jouhsen-bündgens machines
- 26. April 2024
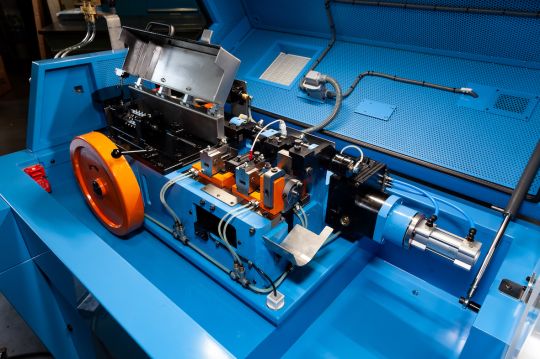
Even Jouhsen-bündgens wire processing machines start to show their age at some point, even if they perform well for a very long time. Efficiency falls and product quality starts to suffer. This is when users need to take action. A general overhaul, also known as a retrofit, can be a good alternative to purchasing a new machine.
Retrofitting is worthwhile
Both in terms of time and costs, a general overhaul can be worthwhile for all Jouhsen-bündgens machines, whether they are used for straightening and cutting, end machining, cold forming or point grinding. “A general overhaul of a machine costs just 60-70% of the cost of a new one,” explains Jouhsen-bündgens Managing Director Dr. Peter Renz. Realistically, companies need to plan around three to six months in advance to procure the necessary parts. The overhaul itself generally takes around four to six weeks. Renz continues: “After this, the customer gets a machine that is good as new and has another 20 to 30 years of service ahead of it, all in record time.”
Overhauled from the ground up
With their basic structure made from solid steel and cast metal, Jouhsen-bündgens machines are built for robustness and extreme durability. But the guides, lubrication system and controls in particular can all suffer over the course of their service lives. Motors and drives can become worn, or sensors can stop working properly. A retrofit can address all these issues. “We’ve seen machines working perfectly even after undergoing a second overhaul,” says Renz. Any machine sent for a retrofit is first disassembled into its individual parts. Each part is then thoroughly cleaned and checked for cracks, with any damaged components replaced. One of the advantages of having Jouhsen-bündgens perform an overhaul is that the company has access to all the diagrams for its machines. Once the replacement parts have been procured and the wearing elements processed, the next step is assembly. The machine is fitted with a new lubrication system, new electrical and pneumatic systems, and a new controller as chosen by the customer.
Proven quality
But do the products made on the retrofitted machine still meet specifications? Customers generally provide sample material, which Jouhsen-bündgens processes using original tools. The products are put through their paces before the retrofitted machine is returned to the customer, who can also perform their own quality checks if necessary. Once all the boxes are ticked, the customer can enjoy using a machine that meets the current EU safety rules.
Peace of mind with a maintenance agreement
Jouhsen-bündgens recommends customers who want to use their wire processing machines and offer excellent product quality over the long term consider a maintenance agreement. This ensures the machines are regularly given a thorough check-up, usually once a year. Over the years, it is therefore possible to observe how wear occurs. The optional maintenance reports document whether the machine will soon be due a full or partial overhaul. “This makes planning a retrofit easier and keeps machine downtime to a minimum,” explains Dr. Renz. He insists that retrofitting a Jouhsen-bündgens machine is always worthwhile when the products it makes are still needed, or if the machine can be easily converted to making products in demand. This is even the case when the machine has to be shipped to Stolberg from abroad, which happens more often than one might think.